Magnetic particle testing
What is Magnetic Particle Testing?
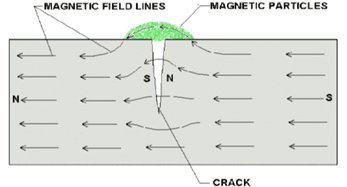
Magnetic Particle Inspection (MPI) uses magnetic fields and small magnetic particles (i.e. iron particles) to detect flaws in components. The only requirement from an inspection standpoint is that the component being inspected must be made of a ferromagnetic material such as iron, nickel, cobalt or some of their alloys.
During Magnetic Particle Inspection the work piece is magnetized. If any defects are on or near the surface, the defects will create a leakage field. The iron particles are suspended in light oil and are applied to the surface of the magnetized part. The particles will be attracted and cluster at the flux leakage fields, thus forming a visible indication that the inspector can detect with ultraviolet light. Magnetic Particle Inspection produces very exact results.
Tilley Pressure Test Technicians are able to not only locate part defects, but also accurately assess their degree of severity. The indication can then be evaluated to determine what it is, what may have caused it, and what action should be taken, if any.
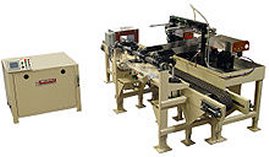
A wet horizontal MPI machine is the most commonly used mass production inspection machine. The machine has a head and tail stock where the part is placed to magnetize it. In between the head and tail stock is typically an induction coil, which is used to change the orientation of the magnetic field by 90 degree from head stock. Most of the equipment is customized and built for a specific application.